Understanding Foam Moulding and Its Benefits
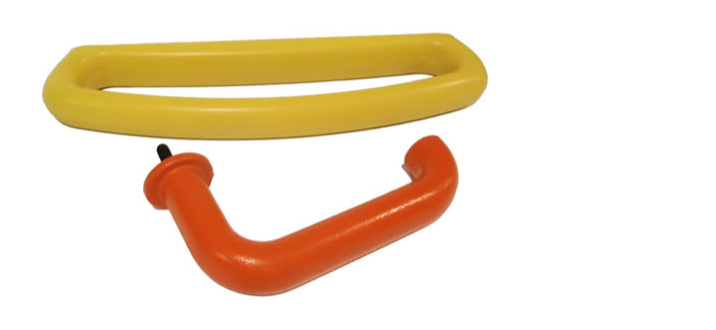
Foam moulding, specifically Polyurethane Foam Moulding, is a versatile process that has gained significant importance in various industries over the years. As a leading technology in the manufacturing of foam products, it provides numerous advantages, such as superior durability, customization, and flexibility. Polyurethane foam, also known as integral skin foam or self-skin foam, is widely used to create products that require a tough, flexible, and aesthetically pleasing surface. At Acoustafoam, we have over 36 years of experience in polyurethane moulding technology, specializing in creating bespoke foam products that meet the highest quality standards.
This article will delve into the world of foam moulding, the benefits of polyurethane foam, its applications, and the various industries that use this technology. We will also explore the different types of foam products produced by Acoustafoam, including integral skin foam, elastomers, impact foam, and more. By the end of this article, you will have a thorough understanding of foam moulding and its integral role in a wide range of applications.
1. The Process of Foam Moulding
The process of foam moulding involves combining two parts of a polyurethane chemical mixture that undergoes a chemical reaction when dispensed into a mould. The material expands within the mould, curing to form a foam product. Once the foam has fully cured, the product is carefully removed, and any excess material or flash lines are trimmed away.
Polyurethane foam moulding is available in several forms, including integral skin, elastomers, and impact foam. Integral skin foam, for instance, forms a tough, tear-resistant skin during the moulding process. This skin provides excellent protection against wear and tear, scratches, and abrasion, making it ideal for products that undergo frequent use. The foam core beneath the skin can vary in hardness, typically ranging from 30 to 90 Shore A, offering different levels of comfort or rigidity depending on the application.
The mould tooling is crucial in creating the desired texture and finish of the foam product. For example, Acoustafoam can chemically etch the mould to give the foam surface a leather-like or other textured appearance. This versatility makes polyurethane foam suitable for a variety of applications in many industries.
2. Benefits of Polyurethane Foam Moulding
Polyurethane foam moulding offers a wide array of benefits, making it the preferred choice in industries ranging from automotive to furniture manufacturing. Below are some of the key advantages:
- Durability and Strength: Polyurethane foam products are known for their exceptional durability. The integral skin provides a strong and flexible surface that can withstand wear, tear, and impact, making them ideal for high-traffic applications.
- Customization: One of the standout features of polyurethane foam is its ability to be custom-moulded into a variety of shapes, sizes, and finishes. Whether you need a leather-like texture or a soft-touch finish, polyurethane foam can be tailored to meet your specific requirements.
- Comfort and Versatility: Polyurethane foam can be produced with varying hardness levels, allowing for the creation of products that are either soft and cushiony or firm and supportive. This versatility makes it suitable for a wide range of applications, from headrests in vehicles to office furniture and toys.
- Lightweight and Flexible: Despite its strength, polyurethane foam is relatively lightweight, which is an advantage in applications such as automotive parts, where weight reduction is essential for fuel efficiency. Its flexibility also allows it to be moulded into intricate shapes, making it an ideal material for custom-designed components.
- Sound and Vibration Dampening: Polyurethane foam has excellent soundproofing qualities. It can be used to absorb sound, making it a valuable material for noise reduction in applications such as automotive interiors and office spaces. It is also an effective vibration dampener, which is particularly useful in machinery and transportation.
3. Applications of Polyurethane Foam Moulding
Polyurethane foam moulding is used in a wide range of industries due to its versatility and adaptability. Here are some of the key applications:
- Automotive Industry: Polyurethane foam is widely used in the automotive sector to produce components such as steering wheels, armrests, headrests, and gear knobs. The foam’s ability to withstand wear and tear while providing comfort makes it a popular choice for interior parts.
- Furniture and Upholstery: In the furniture industry, polyurethane foam is commonly used for seating applications, including cushions, armrests, and backrests. Its ability to provide both comfort and support has made it a staple material in the production of high-quality furniture.
- Marine Industry: The marine sector also benefits from polyurethane foam, particularly in the manufacturing of products such as boat cushions, upholstery, and safety equipment. The foam’s durability and resistance to water make it an ideal choice for marine applications.
- Safety Products: Polyurethane foam is also used in safety products, such as helmets, padding for sports gear, and protective equipment. Its impact-absorbing properties help reduce the risk of injury in various high-risk activities.
- Gaming Industry: The gaming industry relies on polyurethane foam for products such as gaming chairs, where comfort and durability are paramount. The foam provides the necessary cushioning for long gaming sessions while maintaining its shape and integrity over time.
- Construction Equipment: Polyurethane foam moulding is used in the production of various components for construction equipment. Its ability to resist heavy impacts and provide insulation makes it ideal for use in machinery and vehicles that operate in tough conditions.
4. Acoustic Barrier Products: Enhancing Sound Insulation
Another significant application of polyurethane foam is in the production of acoustic barrier products. These flexible, sound-insulating products are designed to reduce airborne noises and minimize impact sounds, thus improving sound insulation. Acoustic barriers are widely used in industries such as automotive, construction, and manufacturing, where noise control is a priority.
Acoustafoam offers a broad range of acoustic barrier products that combine the flexibility of foam with advanced soundproofing properties. These barriers are available in various forms, such as sheets, die-cut pieces, and water jet cut products, and can be customized to meet the specific needs of different applications. They can also be combined with acoustic foams to create bespoke laminates that provide superior sound absorption and transmission loss.
In addition to sound insulation, Acoustafoam’s acoustic barriers also offer excellent anti-vibration properties, making them ideal for use in environments where machinery or heavy equipment generates vibrations. Common applications include noise reduction in automotive cabins, construction vehicles, and industrial machinery.
5. Foam Conversion: The Key to Customization
Foam conversion refers to the process of transforming foam materials into custom products through various techniques such as cutting, moulding, laminating, and profiling. At Acoustafoam, we utilize advanced foam conversion methods, including CNC profiling, water jets, and die cutting, to create bespoke foam products tailored to meet the unique requirements of our clients.
Foam conversion is particularly important in industries that require highly specialized foam products. For example, in the automotive industry, foam conversion can be used to create custom cushioning for seats, headrests, and armrests. In construction, foam can be converted into thermal insulation materials or soundproofing solutions.
The flexibility of foam conversion allows us to support a wide range of applications, from simple foam sheets to complex, multi-layered acoustic solutions. By utilizing a combination of different foam types such as polyurethane foam, polyethylene foam, and polystyrene foam, we can offer tailored solutions that meet the specific needs of our clients.
Read also: Commercial Cleaning Services for Real Estate and Property Management
6. Conclusion
Polyurethane foam moulding is a highly versatile and valuable manufacturing process that plays a critical role in many industries. From its durability and customization capabilities to its soundproofing and vibration-dampening properties, foam moulding offers numerous benefits for various applications. Whether you’re in the automotive, furniture, marine, or construction industry, polyurethane foam can be tailored to meet your specific needs.
At Acoustafoam, we take pride in our 36 years of experience in polyurethane moulding technology and foam conversion, delivering high-quality products that meet and exceed customer expectations. With our expertise in creating bespoke foam products, we are well-equipped to provide innovative solutions to complex challenges across diverse sectors.
By understanding the capabilities of foam moulding and the various applications of polyurethane foam, businesses can make informed decisions when selecting the right materials for their products. Whether you require integral skin foam for automotive interiors, acoustic barriers for noise reduction, or custom foam components for industrial use, polyurethane foam moulding offers a wide range of possibilities to enhance product performance and quality.